Traditional and sometimes highly diverse breakdown situations make up our main body of work and are highly familiar to us. It is important to master the inner life of the entire machine in terms of mechanics, electricity and control – this is how we get the machines up and running again!
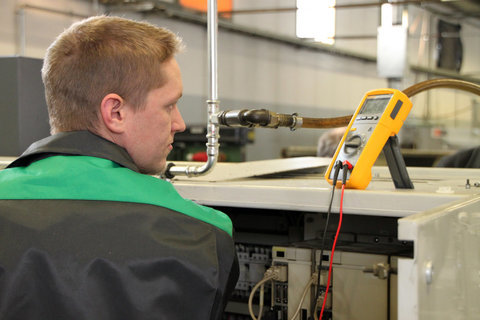
We are familiar with the most common controls and their troubleshooting diagnostics.
We use e.g.
- Heidenhain PWM20 to diagnose, position and adjust linear encoders and pulse-output rotary encoders
- Oscilloscopes, a Fluke Installation Tester, insulation testers, a thermographic camera, inductive sensor testers etc.
- 2 devices for measuring the locking force of a tool, ISO40/50, Capto C6 and HSK 63A
- Chuck compressive force measure
- Various frame and linear stones and test bars for geometry measurements using traditional methods
- Renishaw XL-80 laser interferometer with advanced options
- Spindle taper grinding machine
- 3R mobile oil cleaning equipment with a particle and water content sensor (sensible and affordable alternative to an oil change when using large volumes of oil)
- And many other self-manufactured tools etc. that we have occasionally needed
Our premises have e.g.
- 2 industrial cleaning machines
- Ultrasonic washing machine
- Steam cleaner
- Surface grinding machine
- Cylindrical grinding machine
- Lathe
- Mill cutter
- Column-type drilling machine
- Belt sander
- MIG welding machine
- Break-in bench for testing spindles
- Bearing heaters, oven, freezer, workshop presses, extractors etc. equipment for standard and more demanding mechanical installations
- Workbenches for electric work with adjustable AC and DC power sources
- Crane capacity 10 tonnes